Heat exchangers are considered the workhorse in chemical plants and refineries. They come in all shapes, sizes, and configurations and are essential in extracting or adding heat to various process fluids. Figure 7.1 (TEMA, 1999), shows various shapes of commonly used heat exchangers.
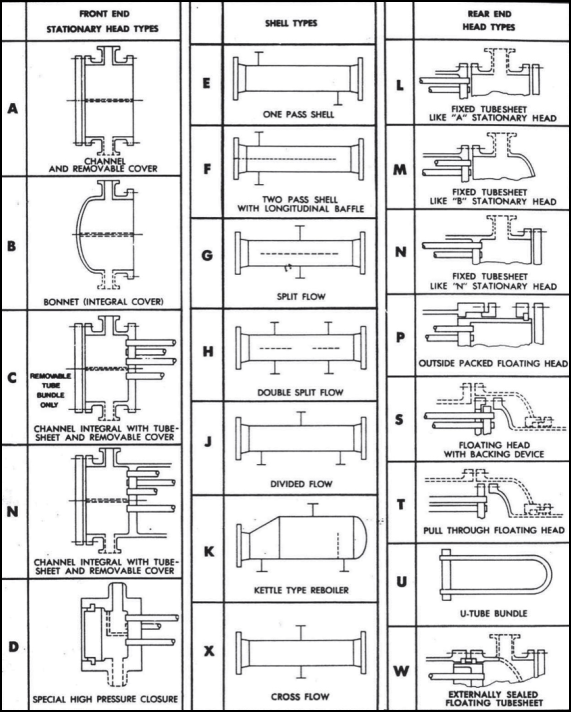
TEMA stands for “Tubular Exchangers Manufacturers Association” and is a set of standards that were developed by leading shell and tube manufacturers. These standards define the style of heat exchanger and the machining and assembly tolerances. One of the advantages of selecting a shell & tube manufacturer that builds to TEMA specifications is that the end-user is assured that they will receive and install a piece of equipment that is built to certain specifications and criteria.
There are 3 major TEMA classifications, which are as follows:
- TEMA C – General Service
- TEMA B – Chemical Service
- TEMA R – Refinery Service
TEMA C is the least restrictive and most widely used. TEMA B and TEMA R are similar in requirements and typically require features like confined gaskets joints, spiral wound gaskets along with some greater minimum thicknesses on some parts.
TEMA designations refer to portions of the unit that make up the complete heat exchanger. IE: TEMA Type BEM would have the “B” representing the front head, the “E” the core or middle section and M representing the rear head designs.